How to approach disruptions in commodity supply chains
Introduction
For the past few decades, there has been a relentless approach to increasing the efficiency of logistics supply chains. While efficiency brings cost savings, it can also reduce supply chain resiliency and leave you more vulnerable to today’s increasing supply chain disruptions.
These disruptions can be especially acute for companies involved with petroleum and natural gas-based commodities, from producers to end consumers. For example, feedstock disruptions will impact refiners, NGL fractionators, and chemical manufacturers; blendstock disruptions will impact refined products and fuel marketers who blend their final products and; fuel disruptions will impact anyone moving products, including crude oil, refined products, NGL and fuel markets, and those who consume fuel, like power generators.
In this post, we will cover some of the risks and challenges of supply chain disruptions and steps that can be taken to mitigate the impacts of those disruptions.
What are the risks, challenges, and impact of supply chain disruptions?
A supply chain disruption is an event that causes an interference in the logistics supply chain that prevents products from moving to and from planned locations, via planned movements and schedules. Supply chain disruptions can be triggered by events like natural disasters, world conflicts, pandemics, accidents, or transportation breakdowns. Without planned product volumes at planned locations, purchases and sales and related contractual obligations may not be able to be fulfilled. Due to interdependencies in today’s global economy, local disruptions can quickly escalate into global product shortages impacting commodity prices globally. As modern life is highly dependent upon those commodities from around the world, even a disruption of 1 or 2 days, or even less than a day for critical feedstocks, can have serious consequences.
Even if a disruption is quickly resolved, there will likely be cost increases due to additional logistics costs arising from transit delays and demurrage if products are stranded at an origin or destination during the disruption. Minor, infrequent, or occasional disruptions are unlikely to damage a company severely. However, a series of minor disruptions can be detrimental and affect the company’s ability to fulfill its contractual obligations which will, in turn, impact its financial performance due to increased costs and missed sales.
If the disruption persists, facilities dependent upon the disrupted product(s) for refining, fractionation, manufacturing, or blending may have to shut down. This will, in turn, cause interference in supply chains for the product(s) being refined, fractionated, manufactured, or blended. Force majeure may be declared on contracts, impacting relationships with counterparties. In the worst case, an extended shutdown could result in financial losses from which, the company may not be able to recover.
Beyond the apparent impact of not being able to receive or produce products, other issues can occur. If the problem comes from the access or supply of a major feedstock or blendstock, facilities might be forced to ramp down or shut down. As a consequence, this could lead to the delivery of all product components to also be slowed or stopped too because many commodity inventories rarely hold more than a few days’ supply of product(s).
Storage capacity for finished products may also become overwhelmed at facilities that are still in operation if the logistical assets they rely upon for transport are stranded or late due to the disruptive event. Even if one thinks they are isolated from supply chain disruption because they deal in completely different product(s), they may see their logistics costs go up dramatically as the logistics companies and assets they usually rely upon shift focus to cover disruptions. In the worst case, some logistics assets, like vessels, may also become unavailable.
Rethink the logistics to approach supply chain disruption
According to Randstand (Cause and effect of supply chain disruptions. | Randstad) “Supply chain shortages across the globe rose by an astonishing 638% in just the first half of 2021.” This trend of frequent disruptions is continuing into 2023 and beyond. Knowing that these disruptions are likely to occur more frequently and likely to have significant operational, customer, and financial impacts, what can a business do?
The first step to addressing the problem is to assess your current and future inventories and contractual obligations across your business’s entire portfolio. Without doing this first step, you will be dealing with the problem less effectively and lose strategic opportunities to mitigate the impacts better or, in some cases, take advantage of the situation and gain market share. A portfolio-wide view of your business involves knowing what you have, where you have it, and what it is worth. When you have this view, you can answer 10 fundamental questions for an effective mitigation strategy:
- Where and when is the business likely to be disrupted?
- What facilities will have to ramp down or shut down, and when?
- What facilities impact the business the most and should be kept operating at all costs?
- Where am I most exposed to not meeting contract obligations?
- Where is there an excess product that could mitigate the shortage?
- Where is there a substitute product that could mitigate the shortage?
- Where is the most profitable place to sell any available disrupted product(s)?
- Where is the least impactful place to declare force majeure?
- What transportation assets are near the facilities facing shortages?
- Where are the alternative sources of products?
It is important to determine all the above, not only when the event occurs but also to factor in the anticipated impacted timeframe. These questions effectively quantify both the impact of the disruptions and potential outcomes from decisions, like failing to meet contractual obligations and in the worst case, declaring force majeure.
Five steps on how to manage supply chain disruptions
Having complete visibility of your business and making decisions in time of crisis is a difficult task. Acting fast on accurate and timely information is key to effective decision-making when risks become reality. Once the situation has been assessed, the following steps can occur to avoid facilities shut down, missed contractual obligations, overflowing storage, or reputational damage:
- Determine where you do or do not need the disrupted product(s)
You need to determine what facilities must be kept operating at all costs that require the disrupted product(s). You also need to determine your value highest-value contractual obligations that are tied to the disrupted products to avoid breaking contractual obligations for high-value customers.Conversely, you should also determine what low-value customers you could afford to reschedule or break contractual obligations related to the disrupted product(s). The freed-up product(s) can help meet your key facility and high-value contract obligations. - Determine how to get replacement product(s) to the locations you need it
Once you have assessed where you need and do not need products, you can now evaluate alternatives to get the same product(s) or substitute product(s) to the required locations looking at both time and costs. It is also essential to evaluate the alternatives for the expected duration of the disruption. An obvious potential source of the product supplies is products left in a facility that is shut down or in facilities with the excess product(s) at a non-impacted location.Related to this is evaluating alternatives for locations where you will not need the replacement product(s). In some cases, one may have to defer or redirect deliveries of other products if throughput cannot be maintained. - Determine the best alternatives and create a plan
After determining the possible alternatives, the next step is to define the best combination of options. This will likely be a combination of redirected, new, and/or canceled movements which could be done via a variety of modes of transport. This combination needs to be put into an execution plan, and approved so it can be quickly executed. It’s important that those in charge have the authority to execute the mitigation plan and act fast. Also, remember that it is often better to execute a good plan rapidly than a fully optimized plan late. This process should take hours, not days.Ideally, scenarios should be created and run periodically to take care of steps 1, 2, and 3. It is unlikely that one would follow a previously created scenario exactly, but it will almost always provide a better starting point. Additionally, doing steps 1, 2, and 3 in a scenario or sandbox environment helps develop organizational skills to create and approve such execution plan rapidly. - Execute the plan
One of the first aspects of the plan will often be trading. This is to mitigate the impact of price increases due to the disruption, and secure products.Once the plan has been approved, it needs to be executed and time is of the essence. Those who are among the first to redirect, cancel, and secure new transportation arrangements will almost always receive more favorable treatment and pricing than those who follow. In some cases, one may be able to lock up most or all the available replacement products and/or available transportation by acting early. This means they can deliver when their competitors cannot and can enable them to gain market share or sell the product to competitors for a significant premium.Finally, part of the plan may be to declare “force majeure” on some contracts. If so, this needs to be done with extreme care to ensure one does not create additional unnecessary legal and counterparty issues which could lead to reputational damage and loss of business.Most would think that execution is the last mitigation step. However, there is another step that is also critical to do when these events occur. - Quantify the impacts of the disruption
It is essential to quantify the impacts of the disruption operationally, financially, and contractually. Knowing the impact help you communicate better with key stakeholders about the disruption. For example, a loss in revenue will be easier to explain when you can quantify what the loss would have been had one not acted quickly enough. Similarly, a gain in market share over competitors can soften the blow of price increases in commodities and transportation to secure needed products. Finally, if the disruption is particularly extreme, and not expected to re-occur for several years, taking the impact out of results can better show the normal performance of a business.
- Determine where you do or do not need the disrupted product(s)
Conclusion
This blog discussed some of the key aspects of why an understanding of your portfolio is key to evaluating the situation when disruptions occur, and some of the steps you could follow to lessen their impacts. Following these recommendations will not eliminate their impacts, but it will certainly leave you better off than you would be by responding in crisis mode without a plan. Merely reacting to the disruption can be very dangerous and, in the worst-case scenarios, result in financial losses that a company may not be able to recover.
Doing all the actions above will also be deemed challenging without a good commodity management solution (CMS). Having processes, workflows, and access to data is crucial to taking these kinds of measures.
ION Commodities is the world’s leading provider of such systems.
About ION Commodities
ION Commodities is the leading provider of energy and commodity management solutions to organizations of all sizes across all industries, commodities, and regions. ION understands that no two companies are the same and offers choices with a comprehensive portfolio of product solutions to address a breadth and depth of business needs.
ION’s extensive product portfolio equips businesses to address current market dynamics for better control and improved visibility into your commodity business operations and risk with accurate data and insights across one’s supply chain.
ION’s innovative suite of products ranges from packaged, multi-tenant SaaS solutions to highly customizable platforms with advanced functionalities for managing marketing, trading, volatility, risk, inventory, scheduling, actualization, settlement, and invoicing processes. ION also has sophisticated value-added solutions for advanced risk analytics, credit and counterparty management, supply chain optimization, and vessel chartering and operations.
Speak to one of our experts today and find out how ION can help transform your business.
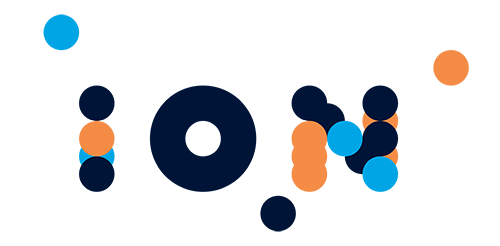
Are you equipped to handle reoccurring commodity market disruptions?
How long will it take your organization to answer the following 8 questions if a disruptive event happened tomorrow?